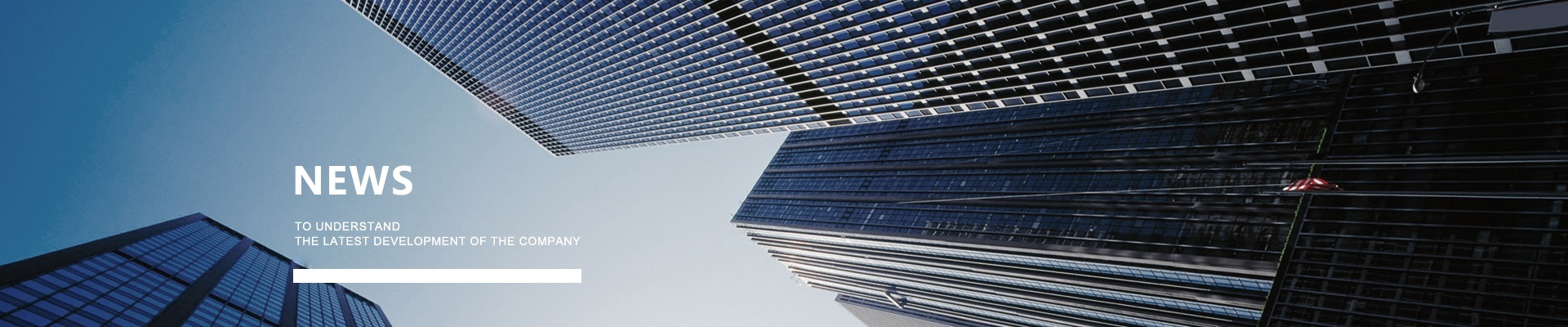
Technical Requirements and Material Selection of Automobile Accelerator Pedal
The accelerator pedal is an indispensable part of the modern automobile power system, and the reliability of the accelerator pedal is one of the main design parameters of the power system. The main function of the accelerator pedal is to control the opening of the engine throttle, thereby controlling the vehicle speed. A reasonable accelerator pedal can promote the simplification of the car's interior, increase the driver's space, and reduce the quality. The material of automobile accelerator pedal develops along the direction of environmental protection, energy saving, material saving, safety and low cost, and has made significant progress represented by lightweight, showing a trend of diversification and diversification.
Automotive power system materials are one of the foundations of automotive design level, quality, quality and other competitiveness. The degree of automobile lightweight mainly depends on the development of automobile material lightweight. In recent years, glass fiber reinforced nylon materials such as PA66 30GF, PA6 30GF, etc. have become a new choice for automobile engine accelerator pedal materials. Glass fiber reinforced nylon materials are of great concern to automobile OEMs and accelerator pedal manufacturers due to their easy modeling, light weight and low cost. In particular, the glass fiber reinforced nylon material has a large degree of freedom in shape design, and the accelerator pedal made of it has good durability, pressure resistance and vibration resistance.
Technical requirements for accelerator pedal
The accelerator pedal is an important part of the automobile power system. In order to meet the safety of the automobile during use, the accelerator pedal should include the following main technical requirements:
a. General requirements
The pedal device shall work flexibly during the whole working stroke without abnormal noise, and the surface of the pedal shall be smooth, uniform and free of defects such as bubbles, cracks, burrs and scratches.
B. Basic requirements
1. Durability
2. Pressure resistance
The positive pole of each circuit of the pedal sensor and the ground shall withstand 12V ± 0.5V for at least 5min.
3. Corrosion resistance
The pedal assembly shall be placed in the neutral salt spray environment with a temperature of 35 ℃ and 5% for 24h, then placed in the environment with a temperature of 60 ℃ and a humidity of 95% for another 12h, and then stabilized at room temperature for 2h before performing the function test.
4. Anti-drop
The pedal assembly shall be dropped from a height of 1m above the ground onto a smooth concrete floor, and the six directional surfaces of each pedal shall be tested separately. A total of 3 pedals shall be used; the tested pedals shall meet the functional test requirements and shall not be damaged or affect the assembly of the pedals.
5. Anti-vibration
6. Pedal strength
7. Dust resistant
The pedal assembly shall meet the functional test requirements after being exposed to a dust environment of 0.88g/m3 for 24h.
8. High and low temperature cycle resistance
The pedal shall be kept at -40 ℃ for 3h, then heated to 85 ℃ for 3h, and then cooled to -40 ℃. As a cycle, the temperature conversion time shall be less than 5min. A total of 6 thermal shock cycles shall be carried out, and the pedal after the test shall meet the functional test requirements.
9. Storage resistance
Place the pedal assembly at -40°C for at least 48h, at room temperature for at least 6h, and then at 85°C for at least 48h. The pedal after the test shall meet the functional test requirements.
10. Low noise
The noise generated during the pedal release back to the initial position at a speed of 0.01 m/s shall not exceed 45dB(A)(measured at the driver's ear, 1350mm from the pedal pad). When the pedal is momentarily released from any position, the noise generated by the rebound shall not exceed 83dB(A), and the noise above 600Hz shall be less than 70dB(A) at any time.
11. Resilience
Fix the pedal on the test bench, move the pedal to the full stroke position and release it instantly. The pedal rebounds to the initial position as a cycle. A total of 1000 cycles are performed. The output signal of the sensor at the idle position is monitored every 100 cycles. The pedal is tested for performance after 1000 cycles.
Material Selection of Accelerator Pedal
a. Development history of accelerator pedal materials
The development course of automobile accelerator pedal materials and corresponding processing technology is: cast iron or cast aluminum parts-stainless steel-die-cast aluminum alloy parts-(nylon) thermoplastic injection parts.
B. Performance comparison of various materials
Now the cast iron or cast aluminum parts, stainless steel parts, die casting aluminum alloy parts, thermoplastic (nylon) injection molding parts performance comparison is as follows.
c. Analysis of glass fiber reinforced nylon materials
1. Lightweight
For the same car, the thermoplastic nylon injection molded parts selected for the accelerator pedal are similar to the traditional material parts in strength and rigidity. The weight index of the accelerator pedal parts is reduced by more than 50% compared with stainless steel parts and aluminum alloy castings. Reduce 30%-40%; the precondition for this comparison is that the effect of structural measures such as increased wall thickness and local stiffeners added to the design to compensate for the stiffness and strength of the new nylon plastic material on its own quality has been considered and taken into account.
2. Design freedom
The glass fiber reinforced nylon material greatly improves the design freedom such as the change of the wall thickness of the parts, the design of the local reinforcing ribs, and the integration with the connecting rod parts.
3. Processing costs
Compared with traditional accelerator pedal materials, the processing cost of thermoplastic glass fiber reinforced nylon accelerator pedal has obvious advantages. Thermoplastic nylon injection-molded accelerator pedal can not only improve production efficiency, but also reduce production costs. The cost of the mold alone can save considerable costs, because the service life of the nylon plastic injection mold is 10 times that of the aluminum alloy die-casting mold; the accelerator pedal and the connecting rod components are integrated for injection molding to reduce the assembly cost of the accelerator pedal; the injection molding manufacturing process The product defect rate of the aluminum alloy casting process is lower, and the system cost is reduced. Some data show that the production cost of glass fiber reinforced nylon injection pedal is 30%-40% lower than that of die-cast aluminum alloy material.
4. Reliability
The working reliability, durability and low temperature adaptability of glass fiber reinforced nylon pedal have passed the certification of major OEMs including Volkswagen, GM, Ford and Geely.
According to the technical requirements of automobile accelerator pedal and relying on the development direction of current automobile technology, Hairizhisheng Technology Co., Ltd. has continuously increased its investment in research and development efforts and funds, and developed a material that can be used for accelerator pedal-A6G04. A6G04 is the company through the substrate selection, processing technology and other technological innovation, performance has been close to the same industry at home and abroad products, has been used and promoted in customers.