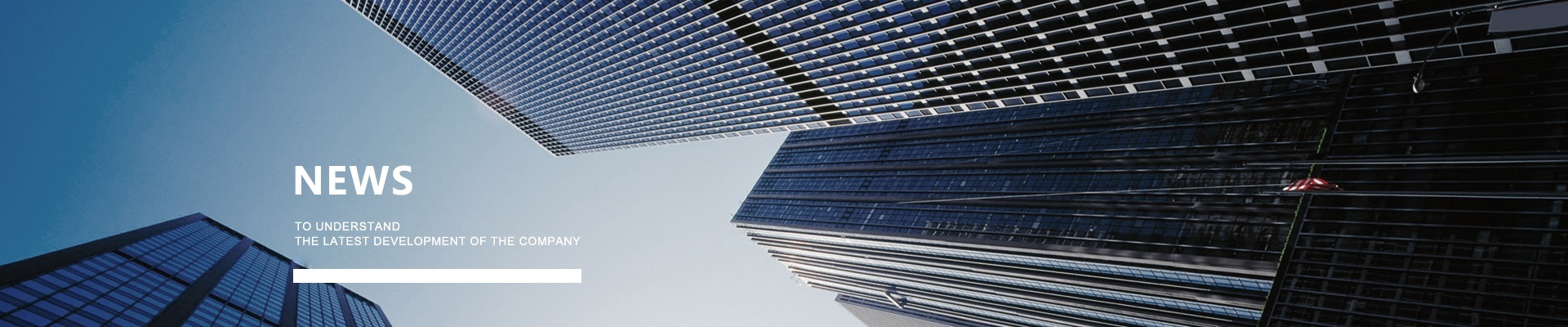
Brief Discussion on Material Selection of TV Shell
Why choose plastic as a TV shell?
You may have such doubts, "Why is the back shell of the TV set made of plastic now? Isn't it more dazzling to use metal?" In fact, not only the back shell is plastic, but also the front panel frame is plastic, but some high-end models will adopt the edge of the frame.
Metal material to enhance the grade of the product.
We all know that metals produce an effect called "electrostatic shielding". It is the outer shell of the conductor that "protects" its interior, so that its interior is not affected by the external electric field. This phenomenon is called electrostatic shielding. Therefore, in order to ensure the strength of the wifi signal, almost all smart TVs are made of plastic.
Requirements for material selection of TV shell
The performance requirements of TV materials are heat resistance, flame retardant, voltage resistance, corona resistance and mechanical performance requirements.
High and low temperature impact requirements
Good high and low temperature impact, to prevent collision, fall after crushing, in order to adapt to the northern winter cold weather, the requirements of the material low temperature impact resistance is better, the general requirements of -30 ℃ low temperature impact resistance.
Environmental protection flame retardant requirements
In order to ensure its safe use, the TV housing requires good flame retardant performance and the flame retardant grade should reach UL 94 V0 grade. The EU ROHS standard eliminates 6 substances in electrical and electronic products, including lead, mercury, cadmium, hexavalent chromium, polybrominated biphenyls and polybrominated diphenyl ethers, which means that plastics containing polybrominated biphenyls and polybrominated diphenyl ethers as flame retardants cannot be used in TV housing materials, I .e. the housing requirements.
Material Processing Fluidity Requirements
The TV housing is a large thin-walled product, and the material requires good fluidity in order to fill the mold smoothly. Materials with high melt index (MFR) shall be selected.
Development Trend of TV Shell Materials
Early, more choice of ABS material. ABS has good comprehensive performance. The material has high mechanical strength, small shrinkage rate and good insulating material. Its electrical performance does not change greatly with the change of temperature and humidity. Like most organic polymer materials, ABS resin is combustible material with low limit oxygen index (LOI) (18.3-18.8) and HB grade according to UL94 standard. When ABS is on fire, it burns fast and releases a large amount of toxic gas and black smoke, which is not conducive to practical application. Therefore, in the past 50 years, people have carried out a lot of research and development on flame retardant ABS. Flame retardant ABS is mainly used in telephone, computer and other electronic and electrical equipment shell (required to meet UL94 V-0 or 5-V standard).
According to different requirements, the LCD TV shell choose different flame retardant ABS. For example, high-gloss non-spraying products exported to Europe usually use high-gloss halogen-free flame retardant PC/ABS alloy, which can meet the requirements of WEEE and the environmental protection requirements of TCO'03 in Europe. And spray-free ordinary products, large-size TVs usually use brominated epoxy resin flame retardant ABS resin to meet the processing requirements of the product. However, small-sized products usually use tetrabromobisphenol A environmentally friendly flame retardant ABS resin to save costs. Export to the United States, or other non-ROHS directive related requirements of LCD TV bracket, electrical box and other internal parts, usually can use decaBDE flame retardant ABS resin.
Since the 1980 s, HIPS has been used instead of ABS. HIPS has good fluidity, and the molding shrinkage rate is about 0.5, which is close to ABS. HIPS can be molded with ABS mold. But the surface gloss of HIPS is not as good as ABS, but in recent years, foreign countries have developed high-gloss HIPS. In terms of cost, the advantage of HIPS is that the price is 20% lower than ABS, and HIPS has become a better choice for TV housing materials. But HIPS flammable, as a TV shell must be modified to achieve UL94 flame retardant V0 level.
The New Trend of TV Shell Material Selection
In the 21st century, with the continuous development of various cost-effective materials, the selection of TV shells will gradually turn to low-cost, lightweight and higher cost-effective. Flame retardant modified PP is expected to become the three generations of TV shell selection materials. As one of the four general-purpose plastic materials, PP has excellent comprehensive performance, good chemical stability, heat resistance, good molding processing performance and relatively low price. However, PP material is flammable, has poor low-temperature impact resistance and large shrinkage rate. Through flame retardant modification, PP products can reach UL94V-0 grade, and can withstand glow wire at 650 ℃ or even 750 ℃ without ignition. Through filling modification, molding shrinkage rate and warpage can be reduced, and rigidity, surface hardness and heat resistance of molded products can be improved. Through modification, low-temperature impact resistance of PP material can also be realized, thus meeting the material selection of TV shell, heat resistance, flame retardant, voltage resistance, high and low temperature impact resistance and high fluidity requirements. Shanghai Risheng has been committed to the modification of engineering plastics for 20 years. The flame retardant PP series product PPTV01 in its plastic safety series has been successfully applied to the fields of electronic appliances and household appliances, realizing the replacement of flame retardant ABS and other products, and realizing the upgrading of products for customers. At present, the PPTV01 flame retardant PP product developed by Shanghai Risheng for TV shell is resistant to heat and oxygen aging, low halogen, low density, low temperature, low impact resistance, low temperature and GWFI960 ℃, hot ball indentation is less than 1.8mm, and has good electrical insulation, chemical resistance, good molding processability, can replace the flame retardant HIPS used in TV shell, to achieve lightweight, higher cost performance.