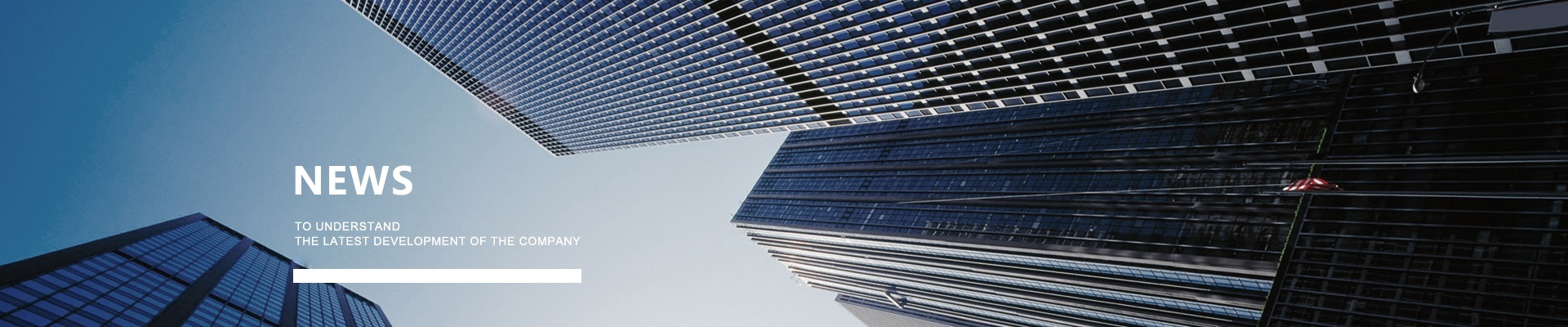
An Old Materials Engineer's Analysis of the Flame Retardancy of Thermoplastic Elastomers (TPS)
The TPS thermoplastic elastomer generally refers to a thermoplastic elastomer containing SEBS (styrene-ethylene-butylene-styrene block copolymer) as a main component. It has the excellent characteristics of both plastic and rubber, can be thermoplastic processing, feel flexible and delicate, anti-aging, high strength, high and low temperature resistance, easy molding, not easy to flow, dimensional stability and design flexibility, suitable for extrusion, injection molding, injection molding, calendering, hollow molding and other plastic molding process, almost all soft products can be used.
However, there are many components in the TPS thermoplastic elastomer formulation system. Due to the differences in the structure and properties of each component, the mechanism is not clear, which brings considerable difficulty to the flame retardant, and there are great safety hazards in the use process, which brings certain limitations to the use of the product.
TPS flame retardant difficulties-three mountains
Difficult one: flame retardant selection is difficult
The compatibility between the flame retardant and the substrate is poor. When the amount of flame retardant in the elastomer system is slightly larger, especially in the halogen-free flame retardant, the elastic modulus, flexibility, mechanical properties and wear resistance of TPS are greatly reduced, the melt fluidity is poor, the elastomer is difficult to form, and the surface is prone to flame retardant migration, which constitutes environmental pollution.
Difficulty two: flame retardant mechanism is not clear
The TPS system is mainly a multi-phase mixed structure of rubber, polyolefin resin, plasticizer and filler. Halogen-free flame retardant polyolefin resin, although there are more mature formulations and examples. However, the flame retardant mechanism of SEBS and polyolefin PP and PE is not the same. It is difficult for a flame retardant to flame retardant a variety of plastic components at the same time.
Difficulty three: plasticizer to reduce flame retardancy
In order to reduce the hardness, TPS often needs to add plasticizer (white oil), usually 26#, 32# white oil and 70# white oil. Due to the difference in the limit oxygen index and fluidity of the four oils, and the natural flammability of the oil material greatly reduces the flame retardancy of the elastomer, how to solve the relationship between plasticizer and flame retardant in the production of low hardness products, how to choose the type of white oil is very important.
TPS flame retardant solution-four step principle
According to my years of research and development accumulation in Shanghai Risheng Company, I have devoted myself to overcoming the above technical difficulties, summarized the four-step principle, and achieved certain results, making the flame retardant TPS elastomer reach UL94 V0, oxygen index 27%, tensile strength greater than 12MPa, and elongation at break greater than 450.
The following four-step principle to share with friends who have been committed to thermoplastic elastomer flame retardant, adhere to the four-step I believe will be inspired by everyone.
The first step: liquid flame retardant not only reduces the hardness but also improves the flame retardancy, reduces the amount of powder flame retardant, can improve the transparency of the product;
Step 2: Relying on the domestic compatibilizer leading enterprise Nantong Risheng for the research and development of SEBS flame retardant system special compatibilizer, improve the compatibility of flame retardant and substrate, improve the precipitation and greatly mechanical properties;
The third step: the process uses special screw distribution to improve the dispersion of flame retardant in the system, improve the flame retardant efficiency and improve the appearance;
The fourth step: the use of new organic silicon flame retardant, condensed phase flame retardant mechanism, the formation of strong oxidation resistance of the cracking carbon layer, improve the flame retardant efficiency.